先日
『陶房青』さんの工房を訪問した際に、ちょうど
『排泥鋳込み』での成形作業をされていましたので、その
『排泥鋳込み』の成形技法についてレポートさせて頂く事にしました。
★ 『ロクロ』と言えばある程度の人でも聞いた事があったり、イメージ出来るものと思いますが、
『排泥鋳込み』に関しては陶芸に関わった事の無い方達には聞いた事もイメージする事も出来ない成形方法だと思います。
この
『排泥鋳込み成形』とは、
『ロクロ成形』とは全く異なる器の成形方法になりますので、これを機会に成形方法の違いについても少しだけ興味を持って頂ければ幸いです。
⇒ こちらの石膏の型は、
『排泥鋳込み成形』で使用する
石膏型になります。
『陶房青』さんの
『排泥鋳込み』の作業所に置いてあった石膏型の中から見つけた、見覚えのある形状の型でした。
こちらの型がいったいどんな製品の型なのかは、レポート最後の方で紹介していますので、まずはその成形方法についてご紹介します。
(通常は磁器の陶土を使いますが、今回は『陶房青』さんの新たな試みとして『黒泥』(陶器)の製品を『排泥鋳込み』で製作しようと作業をされているところにお邪魔させて頂きましたので、そのまま『黒泥』の陶土を使用しての作業工程でご紹介させて頂きます)
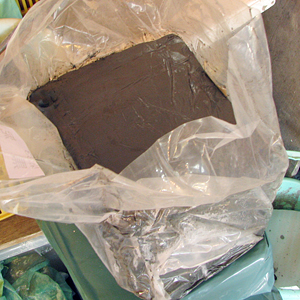
まずは、使用する
粘土(陶土)ですが、通常は
磁器の陶土ですので、もっと白い色をしていますが、今回は
『黒泥』のため当然通常の磁器の陶土と違い『黒』い色をしています。
ロクロ成形や機械ロクロ成形をする場合は、この状態のままで成形をしていきますが、
『鋳込み成形』の場合には
陶土をドロドロの液状にする必要があるため、上の陶土に水やケイソウなどを混ぜて撹拌し陶土を一旦ドロドロの液状にする必要があります。
(撹拌機を使い陶土を液状化しているところです)⇒
このようにして液状化した陶土を、
←『じょうろ』で石膏の型に流し込みます。(すでにこの作業工程が終了した後での撮影でしたので)画像では陶土を
排泥してしまった状態ですが、
本来は石膏の型いっぱいに液状の陶土を溜めた状態にします。
そして、この溜めた状態で2〜3分ほど置くと、
石膏が陶土の水分を吸い、石膏と陶土の接触部分から少しずつ陶土が固まっていきます。
この時の2〜3分の時間の違いで、器の厚みに違いが出て来ますので、作品毎に意図する厚みになるよう時間を計って
『溜泥』します。
▲ 上の行程で2〜3分ほど置いたものを、今度は石膏の型から不要な陶土を
『排泥』します。
⇒
『雨どい』のような
『排泥』用の枠に型を逆さまにして立てかけ、しばらくそのまま放置して不要な陶土を奇麗に
『排泥』させます。
もうお分かりかと思いますが、この作業から
『排泥鋳込み』と言われる訳です。
『排泥』した型を、生地が乾燥するまでしばらく置いておきます。
(←画像上の状態)
このとき陶土の種類によっても乾燥させる時間にかなり違いがあるそうで、一般的な
磁器の陶土の場合はそれほど時間は必要としないようですが、
陶器(土物)の陶土の場合は丸1日乾燥させないと、型から生地を上手く外す事が出来ないそうで、その辺も作品の性質・特徴と相談をしながら手探りで調整する必要があるのだそうです。
そうして、型から外した生地が画像手前のものです。(破損した生地しかなかったので割れた生地の画像で失礼しております)
そして、
石膏から外した生地の状態でもさらに乾燥をさせる必要があります。特に
『鋳込み成形』は陶土に水分などを加えて液状にしているため、尚更十分な乾燥を必要とする訳ですが、この乾燥の作業も陶土の種類によって乾燥させる時間に違いがあり、無理をして天日で乾燥させると生地が歪んでしまうこともあり、
ゆっくりと時間をかけて乾燥させる必要があります。そうやって生地が奇麗に乾燥し、ようやく生地の完成です。
ここまでの行程を見るだけでも、器の生地ひとつ作るだけでも大変な手間と時間が掛かって作られている事がご理解頂けるかと思いますが、ここまでの行程はあくまでも生地を作るまでの行程であって、さらに
『素焼き焼成』『染付け絵付け』『本焼き焼成』『錦絵付け』『錦焼成』と必要な作業行程を経て、やっと作品が出来上がるわけです。
★『排泥鋳込み』の特徴は、器の生地の厚みを均一に、また、厚くも薄くも調整して成形出来るところです。また、柔らかい陶土を使用するためか、器の表面に柔らかい味わいが生まれる事も魅力のひとつかも知れません。
高圧を掛けて石膏の型に陶土を注入し大量に生地を生産する事が出来る
『圧力鋳込み』の成形に比べると、
『圧力鋳込み』の製品は、使用する石膏型の消耗の度合いで製品の厚みが変わってくる欠点や、圧力を掛けて成形するためか硬く冷たい印象を受ける製品になるケースが多いような気がしますが、
『排泥鋳込み』で作られる製品は、その製品にマッチした厚みに生地を調整することが出来たり、より柔らかな味わいを感じさせる仕上がりに成形出来るメリットがあるような気がします。
(参考記事:圧力鋳込み成形の技法)

サイトに出品中のこちらの
『陶房青』さんの作品は、すべて
『排泥鋳込み成形』で作られた製品です。そのそれぞれの製品が薄く味わいのあるフォルムに成形されているのが分かると思います。
★ 今回のレポートを取材して、一番の驚きと感動を受けたのが
『陶房青』さんの
『古染野バラ角盛鉢』の製品でした。
薄く上品に成形され、また独特の柔らかなフォルムが、商品として採用した当時も大変印象的でしたが、その特徴的な器の形状でありながら、重ねた時に奇麗に重なるその姿を見て、実は恥ずかしながらこの製品は
『圧力鋳込み』で成形された製品だとばかり思い込んでいました(汗)
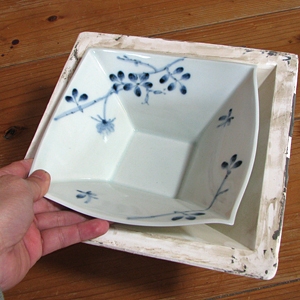
今回
『排泥鋳込み成形』のレポートをするために訪れた『陶房青』さんの工房で、この
『古染野バラ角盛鉢』の石膏型を見つけ、この製品が
『排泥鋳込み』で作られていたという事を知った時も驚きでしたが、さらにその型の形状を見てさらに驚きでした。
←作られている石膏の型はほぼ直線的な四角形で、器の生地も型同様直線的な形状なのですが、焼成されて完成した作品は、何とも言えない味のある曲線のフォルムに仕上がっています。
この器の形状も、
焼成時に変形する事を計算に入れてデザインされている事を知り、デザインの妙というか、成形方法とデザイン力・発想力、そしてそれを実現する技術力、すべてが揃ってこそ作る事が出来る製品なのだなと実感いたしました。
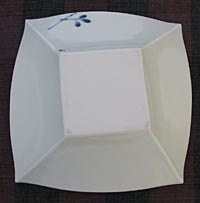
こちらの画像
⇒は
『古染野バラ角盛鉢』を底から見たところですが、
底の四角と渕の四角がほんの少し捻って成形されている事が分かると思います。このようなちょっとしたデザインの工夫にも計算し尽くされたセンスの良さが感じられます。
このような作品に触れると、あながち
『手作りの作品の方がすべて良質・上質』だとは言えないように思える時があります。
色んな成形方法があり、その成形方法をいかに活かしてそれにマッチしたデザインを生み出すか、そしてそのようにして生み出された製品は、
どんな成形方法であれ魅力的なものは魅力的である。今回のレポートを通してそのような思いを強く感じました。
<排泥鋳込み 一口メモ>
『排泥鋳込み成形』で成形する製品の中で、特徴的なものが
『急須』『徳利』など
『袋物』と呼ばれる製品です。
こちらの『型』
⇒は、
『陶房青』さんの
『片口』の製品の石膏型になります。
▲上の
『角鉢』などのような形と違い、口がすぼまったような形状
(袋型)の器は、そのままでは石膏型から生地を取り外す事が出来ないため、
←このように
石膏型を上手く切り離して作る事で、生地を取り外す事が可能になります。
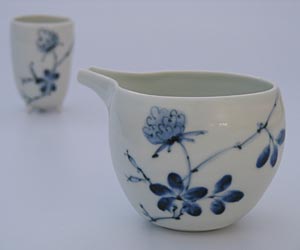
このように手作りでは作れても、
『機械ロクロ』などでは成形出来ない
(袋型の)形状の製品でも、鋳込み成形を使えば型を使って成形する事が出来ます。

サイト出品中のこれらの製品が
『袋物』と呼ばれる
『排泥鋳込み成形』で成形された製品になります。
※ 今回のレポートは『陶房青』さんの工房にて取材をさせて頂きましたが、今回は新商品の製作をするために試作品を製作する過程で自社で器の成形をする必要があったために、このように『排泥鋳込み』での成形作業をされていたのですが、『陶房青』さんでこのように何時も『排泥鋳込み』の成形作業をされているのかと言うとそうでは無く、通常は商品化された製品については、外注で下請けの『生地や』さんに成形をお願いして製作されています。でも、このように大変手間の掛かる成形については『生地や』さんでも高齢化が進んでしまい、その後継者が居なくなって来ているのが現状のようです。
大量生産・大量消費、そして、何でもかんでも無駄を省き効率化・機械化・コストダウンが推奨されて来た価値観が、少しずつ疑問視され始めた現在、手間を惜しまず、無駄を楽しむ、そんな昔ながらの価値観が少し見直され始めている事を感じ、ちょっと手間の掛かる成形方法でも見直されてくる事を願っている隠者です。
★ 関連記事
- 磁器成形方法の種類
- 型打ち成形の技法
- 圧力鋳込み成形の技法
- 細工の職人(機械ロクロ成形の技法)
- ゴッドハンド『ロクロの職人』(ロクロ成形の技法)